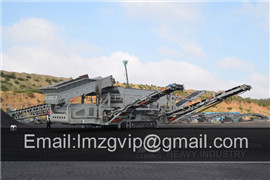
How Is Cement Produced in Cement Plants Cement
1130 Nowadays, the dry process is the most popular cement making process which is widely adopted by cement plants all over the world for its great advantages in energy saving and environmental protection. Cement Making Process. The cement making dry process includes Cement Production Process Cement Manufacturing,825 Cement grinding: The clinker is taken from the clinker silo and sent to the feed bin where it is mixed with gypsum and additives before entering the cement grinding plant. In the Cement Making Process Cement Production Process,Clinker calcination is the most important stage in the cement making process, and it is also a stage with high energy consumption and large gas emission. To produce one ton of cement
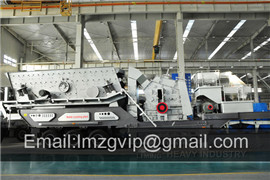
Cement Manufacturing Process: 6 StepsTo Make Cement
127 In the real cement production line, we detail the cement manufacturing process in six steps, including crushing, raw meal grinding, homogenization, preheating and clinker How Cement Is Made,The most common way to manufacture portland cement is through a dry method. The first step is to quarry the principal raw materials, mainly limestone, clay, and other materials. After Cement Manufacturing Process: How the Cement is Made?,2 All the cement plants set up after 1980 use the dry process for the manufacture of cement. In this process, the calcareous materials such as limestone are crushed and stored in

White Cement Manufacturing Process: 6 Steps White
Just like general cement manufacturing plant, the white cement manufacturing process can be generally divided into six steps: Crushing: carbonate composition mostly uses primary How Cement is Made Cement Manufacturing Process,1130 There are six main stages of the cement manufacturing process. Stage 1: Raw Material Extraction/Quarry The raw cement ingredients needed for cement production are Cement Production an overview ScienceDirect Topics,The cement production process, for example, starts with mining of limestone, which is then crushed and ground to powder. It is then preheated to save energy before being transferred to
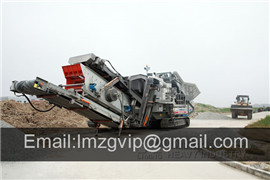
Cement Making Process Cement Production Process
Clinker calcination is the most important stage in the cement making process, and it is also a stage with high energy consumption and large gas emission. To produce one ton of cement clinker, it needs to consume 1.58 to 1.621 tons of raw materials, 0.100.12 tons of coal, and emit about 1 ton of carbon dioxide.Cement Plant an overview ScienceDirect Topics,The original process at the Ramla cement plant to produce cement from limestone, which is the base material of cement, was a socalled wet line process. The original wet line had a capacity of 1,800 TPD (Tons Per Day). The first new production line producing cement through a socalled dry line process was commissioned in 1994.Cement Euipment Overview Cement Making Machines,927 In general, we can divide the cement production line into three main steps: raw material preparation of cement, clinker production, and cement grinding. Each step has some cement manufacturing machines, such as raw mill, cement crusher, cement mill, cement kiln, cement cooler, cement dryer, cement silo, cement packer, etc.
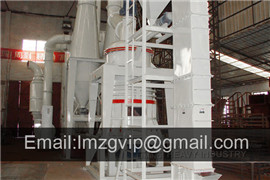
Wet Process of Cement Manufacturing Cement Plant
At cement plant, according to different raw materials preparation methods, cement manufacturing can be divided into the dry process (including semidry process) and wet process (including semiwet process). Next, we will discuss the wet process of cement manufacturing in details. The Diagram of Cement Manufacturing ProcessTypical cement manufacturing process flow ,Finally, during the cement grinding and distribution process, firstly the cooled clinker is ground with around 5% of gypsum and other 17 JRTE cementitious materials to form the final.Cement manufacturing components of a ,Cement is typically made from limestone and clay or shale. These raw materials are extracted from the quarry crushed to a very fine powder and then blended in the correct proportions. This blended raw material is called the 'raw feed' or
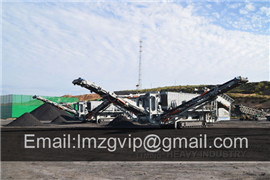
cement Extraction and processing Britannica
There are four stages in the manufacture of portland cement: (1) crushing and grinding the raw materials, (2) blending the materials in the correct proportions, (3) burning the prepared mix in a kiln, and (4) grinding the burned product, known as “ clinker ,” together with some 5 percent of gypsum (to control the time of set of the cement).Cement Manufacturing Machine Cement Making ,At present, most of the cement vertical mills in the market merge crushing, drying, grinding, and grading transportation into a single. They mainly use the grinding disc and rollers to compress clinker particles for realizing the reduction of grain size with small dust pollution.Raw mill Cement Plant, Cement Equipment,In the cement manufacturing process, raw mill in cement plant grind cement raw materials into the raw mix, and the raw mix is sent to the cement kiln to make cement clinker, next, clinker and other admixtures will be ground into finished cement by cement mill.
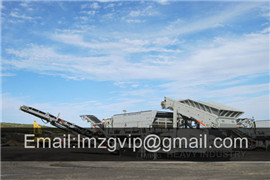
Turning cement green with XRD World Cement
1125 The manufacture of ordinary Portland cement starts by mining and then grinding raw materials that include limestone and clay into a fine powder called raw meal. It is then heated to a sintering temperature as high as 1450°C in a cement kiln. The resulting clinker is ground to a fine powder in a cement mill and mixed with gypsum to create cement.Steps of Cement Production Process Flyer Cement Silo,927 The rotary kiln is a huge rotating furnace as the heart of cement making process. Here, raw materials are heated up to 1450℃. This temperature begins a chemical reaction so called decarbonation. In this reaction materials (like limestone) release carbon dioxide. High temperature of the kiln makes slurry of the materials.Cement Plant an overview ScienceDirect Topics,The original process at the Ramla cement plant to produce cement from limestone, which is the base material of cement, was a socalled wet line process. The original wet line had a capacity of 1,800 TPD (Tons Per Day). The first new production line producing cement through a socalled dry line process was commissioned in 1994.
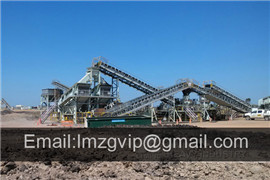
Cement Plant Process Equipments: Cement Plant
121 Cement Plant Manufacturers: Turnkey Plant Equipment Suppliers, Material Handling Equipments Contact 9811141400 for any Cement Plant Eqnquiry Home; form a rocklike substance that is ground into the fine powder that we commonly think of as cement. Process of cement plant is closely controlled chemical combination of calcium,(PDF) Cement Manufacturing ResearchGate,129 Cement plants are usually located closely either to hot spots in the market or to areas with . Figure (5): The Wet process of cement (Mahasenan, et.al 2008) 4.2 Semidry process .Cement manufacturing components of a ,Cement is typically made from limestone and clay or shale. These raw materials are extracted from the quarry crushed to a very fine powder and then blended in the correct proportions. This blended raw material is called the 'raw feed' or
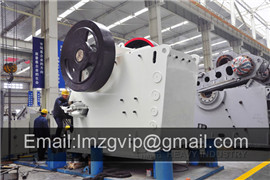
Manufacture of Portland Cement Materials and
a) Dry Process The both calcareous and argillaceous raw materials are firstly crushed in the gyratory crushers to get 25cm size pieces separately. The crushed materials are again grinded to get fine particles into ball or tube mill. Process flow diagram for the cement manufacturing ,A composition of the two most commonly used mineral additives, i.e., fly ash (FA) and silica fume (SF), in combination with nanosilica (nS), has been proposed as a partial replacement for ordinary.The Environmental Impacts of the Cement ,71 Concrete however, has two processes to production that has not changed from its inception. The wet and dry processes both require blasted raw material, a crushing and burning process to create the finished product. In an
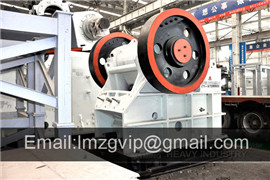
Cement processing equipment Schenck Process
Traditional cement production is based on the push principle of making and storing goods ahead of demand, which is costly and inefficient. Our MULTICOR blending system makes the sustainable cement revolution possible by enabling you to switch to the pull principle so you only produce goods on demand, and to order.Cement Manufacturing Machine Cement Making ,At present, most of the cement vertical mills in the market merge crushing, drying, grinding, and grading transportation into a single. They mainly use the grinding disc and rollers to compress clinker particles for realizing the reduction of grain size with small dust pollution.,