
Analysis of EnergyEfficiency Opportunities for the Cement
2009101 Sixteen NSP kiln cement plants were surveyed regarding their cement production, energy consumption, and current adoption of 34 energyefficient technologies and measures. Energy Efficiency of Rotary Kilns LinkedIn,87 Higher industrial standard is appr. 1.250°C and maximum standard is normally 1.600°C. So for processing tires at 500°C (temperature P1) and a heating gas temperature of Increasing Energy Efficiency and Reducing Emissions from ,201171 A new suspension preheater/precalciner (NSP) rotary cement kiln at one cement manufacturing facility (referred to as Shui Ni 1 in this report) and a vertical shaft kiln (VSK) at
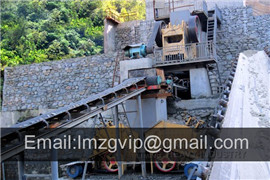
Energy Efficiency Improvement Opportunities for the
1130 The analysis of cement kiln energyefficiency opportunities is divided into technologies and measures that are applicable to the different stages of production and Rotary kiln Cement ABB Drives,Efficiency. Everything counts with high quality clinker. Highlights. Optimization of kiln speed and production flow; Minimized energy use; Maximized production volume; Minimized maintenance costs; Dynamic torque regulation; Reduced [PDF] Energy optimisation of vertical shaft kiln operation ,The technology process usually takes place in shaft or rotary kilns, where the dolomite stone, CaMg(CO3)2, is subjected to a high temperature heat treatment. The calcination of the

Energy Consumption Benchmark Guide: Cement Clinker
1125 The industry has achieved additional energy efficiency gains by using preheaters and precalciners. These technologies have helped the industry reduce its energy consumption Research on Online Monitoring of Energy Consumption of ,Abstract: For the heat balance and thermal efficiency calculation of the cement rotary kiln firing system, the heat of cement clinker formation plays an important role in energy consumption. In ENERGY STAR Focus on Energy Efficiency in ,Duke University evaluated the improvement in the cement industry’s energy performance over a 10year period. Important findings include: Energy intensity improved 13 percent The energy performance of the industry’s least efficient
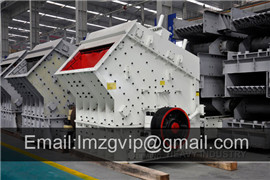
Energy Consumption Benchmark Guide: Cement Clinker
2011112 Present and Future Use of Energy in the Cement and Concrete Industries in Canada. Prepared for EMR Canada, Ottawa. Three dry process kilns have also been shut down during Rotary Kiln an overview ScienceDirect Topics,A. A Boateng, in Rotary Kilns (Second Edition). 10.4 The CementMaking Process. Rotary kilns are synonymous with cement making, being the workhorses of this industry. There are many types of rotary kiln arrangements for producing cement clinker with each incremental design goal aimed at improving energy efficiency, ease of operation, and product quality and minimizing Shaft Kiln, Vertical Shaft Kiln, Vertical Kiln Cement Kiln ,Production Capacity: 60400 t/h. Power: 2255 KW. Application: VSK cement plant. ! Shaft kiln, also known as vertical kiln, vertical shaft kiln, is a vertical and fixed clinker firing equipment. The raw meal ball with coal is fed into cement kiln from the kiln crown, and raw meal ball moves from top to bottom, air move from bottom to top.
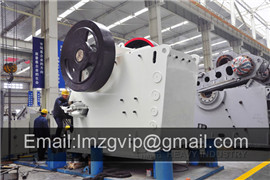
Energy Efficiency of Rotary Kilns LinkedIn
87 Higher industrial standard is appr. 1.250°C and maximum standard is normally 1.600°C. So for processing tires at 500°C (temperature P1) and a heating gas temperature of 950°C you have an energy.ENERGY AND EXERGY ANALYSIS OF CEMENT ROTARY KILN,The average operational data for the rotary kiln is collected for the winter period in the December month of the for the rotary kiln situated at Gujarat Sidhee Cement Ltd, Morasa, GirSomnath, Gujarat, India for the numerical calculations. This paper reviewed mass and energy balance and analysis, exergy analysis for the dry[PDF] Energy optimisation of vertical shaft kiln operation ,Energy optimisation of vertical shaft kiln operation in the process of dolomite calcination V. R. Filkoski, J. Petrovski, Zlatko Gjurchinovski Published Materials Science Thermal Science The essential part of the refractory materials production on a basis of sintered dolomite as raw material is the process of dolomite calcination.
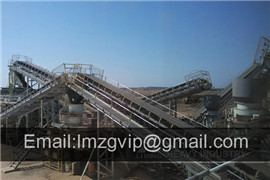
Energy Consumption Benchmark Guide: Cement Clinker
1125 The cement industry's total energy demand increased by 9.3 percent. Clinker production, however, rose by 26 percent. Therefore, energy use per tonne of clinker decreased by 14 percent over the nineyear period.Energy Consumption Benchmark Guide: Cement Clinker ,2011112 Present and Future Use of Energy in the Cement and Concrete Industries in Canada. Prepared for EMR Canada, Ottawa. Three dry process kilns have also been shut down during the decade, but average kiln capacity has increased by 34 percent, further contributing to gains in energy efficiency. Kiln Type Average Fuel Consumption (GJ/t)Energy Efficiency Potential for China’s Cement Industry: ,826 China’s cement industry, which produced 1,868 million metric tons (Mt) of cement in 2010, accounts for nearly half of the world’s total cement production [1]. Nearly 40% of China’s current cement production is from relatively obsolete vertical shaft kiln (VSK) cement plants, with the remainder from modern rotary kiln cement plants,
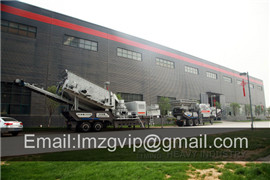
ENERGY STAR Focus on Energy Efficiency in
Duke University evaluated the improvement in the cement industry’s energy performance over a 10year period. Important findings include: Energy intensity improved 13 percent The energy performance of the industry’s least efficient ENERGY STAR Guide for the Cement Industry,1125 ENERGY STAR Guide for the Cement IndustryEnergy efficiency of China's cement industry ScienceDirect,199571 The potential is good for renovating most verticalkiln plants to improve their energy intensity 10–30% while substantially increasing their capacity and reducing pollution, all at los cost. Stateoftheart precalciner kilns offer small energyefficiency advantages, but important environmental and productquality advantages over improved
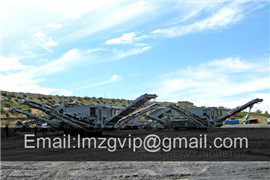
VSK Cement Plant Vertical Shaft Kiln Cement Plant
VSK cement plant is short of vertical shaft kiln cement plant, it is mainly applied for small scale cement plants.As the name suggested, the core equipment of the cement plant is vertical shaft kiln.To meet various needs of clients, we supply different sizes of VSK cement plants, such as 50 TPD, 65 TPD, 75 TPD, 100 TPD, 150 TPD, 200 TPD, and 300 TPD.Modeling of Rotary Kiln in Cement Industry,Description of Cement Rotary Kiln A simple system for cement rotary kiln is shown in Figure 1. Rotary kiln is basically a cylinder of length 50 120 m (modern kilns) and 3.5 to 6.5 feet in diameter. During kiln mainly on how Cement Manufacturing Machine Cement Making ,The shaft kiln is also called a vertical kiln. Compared with cement rotary kiln, it is a standing and nonrotating cylindrical cement kiln, which can also be used in wet cement production line and dry cement production line. The interior of the shaft kiln is divided into preheating zone, calcination zone, and cooling zone from top to bottom.
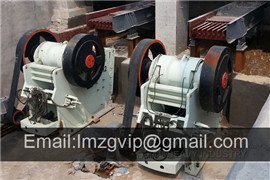
Cement Kilns: Design features of rotary kilns
421 The rotation of the kiln lifts the feed up the side of the kiln, and the energy required to maintain its centre of gravity above the lowest (6 o'clock) point is the main component (8090%) of the energy consumed. VSK Cement Plants Manufacturers, Vertical Shaft Kiln ,824 VSK (Vertical shaft Kiln) Cement Plant Ashoka Group offering Vertical shaft kiln cement plants high efficiency, cost effective, energysaving Cement plants based on VSK technology designed and developed by our efficient and dedicated team of various individuals. VSK Cement plant manufacturing from 50 TPD to 300 TPD on turn key basis Energy Consumption Benchmark Guide: Cement Clinker ,1125 The cement industry's total energy demand increased by 9.3 percent. Clinker production, however, rose by 26 percent. Therefore, energy use per tonne of clinker decreased by 14 percent over the nineyear period.
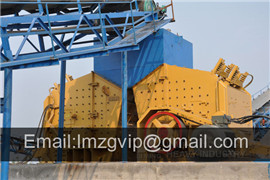
VSK Cement Shaft Kiln for sale 91175766
Vertical Shaft Kiln for sale, Quality VSK Cement Shaft Kiln on sale of Henan Zhengzhou Mining Machinery CO.Ltd from China.Energy Consumption Benchmark Guide: Cement Clinker ,2011112 Present and Future Use of Energy in the Cement and Concrete Industries in Canada. Prepared for EMR Canada, Ottawa. Three dry process kilns have also been shut down during the decade, but average kiln capacity has increased by 34 percent, further contributing to gains in energy efficiency. Kiln Type Average Fuel Consumption (GJ/t)Energy Efficiency Potential for China’s Cement Industry: ,826 China’s cement industry, which produced 1,868 million metric tons (Mt) of cement in 2010, accounts for nearly half of the world’s total cement production [1]. Nearly 40% of China’s current cement production is from relatively obsolete vertical shaft kiln (VSK) cement plants, with the remainder from modern rotary kiln cement plants,